Introduction
Agriculture plays a fundamental role in the economic development in agricultural countries, where its main function is to provide food and the necessary resources for other activities. The modernization, the study, and the contributions made to this field are of great importance so that the undeveloped countries carry out the production and exportation of products. This work carried out seeks to contribute to this branch, saving water and analyzing each plant in the crop. Controlling the use of water in crops allows for better crop performance [1].
In undeveloped countries, most crops do not have a smart irrigation system to control the water estimation, which increases the probability of a manually hydric estimation. Then, crop irrigation is performed without taking into account the needs and ideal factors for each plant, such as evapotranspiration, temperature, humidity, etc. The evapotranspiration is calculated with the water evaporation and transpiration. Manual irrigation can generate a lot of waste since irrigation is done with a hose sporadically. Depending on the plant species and crop diseases, the amount of water in each plant tends to vary. Sometimes it is the soil that absorbs most of the liquid instead of the plants since the plants need a certain time to consume the water.
Generally, hand watering is done until the soil has a large amount of water. However, depending on the type of plant the water irrigation must be equilibrated, several studies show the analysis of crops variating the water [2] [3], in order to establish a goodness result in the crop, es very important to calculate the water. Depending on the species, some plants consume water faster than others. In most cases, hydroponic crops are grown in urban spaces, in some cases, people do not have the time or the knowledge to make a water estimation; in some cases, water is simply applied without taking into account the ideal factors of the plants and the soil. The water resource in a country becomes essential when there is not a good distribution of soil or space [4]. Thus, the hydroponic crops come about in order to perform the use of soil and space in the urban.
In this work, we carry out the implementation of a prototype using components of software and electronic devices. The prototype can perform the function of estimating and watering the plants, measuring the different factors, this is done by moving the device to each of the plants that are in the crop and obtaining the required values, which will allow us to calculate the necessary water. To solve cost issues, the prototype is transported to each plant and the pertinent measurements are made, thereby saving the purchase of sensors per plant. An interface was created so that the farmer in charge can remotely control the device and manage the irrigations. We use the tomato crop as a case study to use the prototype implementation. In addition, this article is an extension of this paper [5] with more specifications in the water estimation.
The paper is structured as follows. Section 1 presents the introduction. Section 2 shows the concepts in the water estimation. In Section 3 we present the related work. In section 4, we explain the approach of this work. In Section 5, the results are explained. Section 6 shows a discussion. Finally, In section 7 the paper concludes.
Hydroponic Crops
In hydroponic crops, there are different methods to replace the soil that are normally used in normal crops. On the other hand, it is very important to keep in mind the water estimation in order to save water. Using this type of crop reduces water use by a considerable percentage, approaching 100%. Also, plant nutrients are not lost but, on the contrary, are continuously stored and recycled. In addition, herbicide use is non-existent and pesticides are natural. [6].
Normally, hydroponic crop irrigation is made by artificial methods or using a design of water pipeline to achieve multiple irrigations in the plants. Without any use of irrigation, the crops are subjected to the availability and reliability of naturally occurring water from floods or rain. Depends on the type of plants, but, in the hydroponic crops, the plants are not exposed to rain instead using pipeline irrigation. There are different types of irrigation methods and techniques used for watering crops. For example, by drip, sprinkler, and microinjection. Each one has a characteristic that makes it the most effective method according to the crop features. Nevertheless, in most cases, the drip irrigation method requires less water than others [7].
Evapotranspiration (ET)
Evapotranspiration is a process that is composed of two sub-processes, which are evaporation and transpiration, each of these two sub-processes being carried out separately. ET is calculated to know exactly how much water is lost to the atmosphere. On the one hand, evaporation is the process where liquid water is converted to steam and removed from the evaporating surface. The water evaporates from surfaces such as rivers, lakes, vegetation, or even the pavement. On the other hand, transpiration consists of the vaporization of liquid water contained in plant tissues [8].
ET is expressed in millimeters (mm) per unit of time and indicates the water lost in a cultivated area. Table 1 shows the factors that influence the ET, which are the climatic variables, the types of crops, and the environmental conditions of the land.
Factor | Description |
---|---|
Climatic variables | Radiation, air temperature, atmospheric humidity, and wind speed. |
Crop | To estimate evapotranspiration, the type of crop used and the stage of development in which it is found must be taken into account. |
Ambient conditions | The inadequate use of essential fertilizers, the parasites found in the soil, and the decrease in its fertility limit the correct development of the crop. |
Reference crop ET (ETo) is the rate of evapotranspiration from a hypothetical reference crop with an assumed crop height of 0.12 m (4.72 in), a fixed surface resistance of 70 sec \(m^{-1}\) (70 sec 3.2\(ft^{-1}\)) and an albedo of 0.23, closely resembling the evapotranspiration from an extensive surface of green grass of uniform height, actively growing, well-watered, and completely shading the ground [9].
In addition, the relation between ETo and ET with a certain surface allows making the relation with other surfaces by removing the process of defining the ET level for each crop and period. Then, it is important to study the rate of ET in the atmosphere regardless of the type of crop and stage considering that the crop does not have water stress or diseases.
The following concepts are required for the calculation of ETo.
Average temperature of the environment (\(T_{hr}\)). This value is obtained by calculating the average between the maximum and minimum air temperature during 24 hours of constant observation.
Saturation pressure of steam at air temperature (\(e^{0}(T_{hr})\)). The pressure generated in the gas phase is known as saturation, which occurs when the temperature of the liquid water and the vapor remain at a constant equilibrium.
Saturation pressure of steam (\(e_s\)). It occurs when we obtain the average result of the saturated vapor pressure with a maximum temperature and the same pressure but at a much lower temperature, this with respect to air.
Relative Humidity (\(RH\)). This process is obtained by dividing the amount of water that the air would contain at a given temperature by the amount of water it could contain if it were saturated at the same temperature.
Actual steam pressure derived from the temperature of the dew point (\(T_d\)). This process occurs when the dew temperature is at its point since this process is the appropriate temperature at which the air must be cooled until it is saturated.
Slope of steam pressure curve (\(\Delta\)). It is the ratio of saturated vapor pressure to temperature.
Atmospheric pressure (\(p\)): During this process, the earth’s atmosphere exerts pressure on the given weight, which is expressed in kilopascals (kPa).
Latent heat of vaporization (\(L_v\)): It is known as the energy used to convert the mass of liquid water into vapor at constant pressure and constant temperatures.
Psychometric constant (\(\gamma\)): It is air as a mixture of two gases that do not interact with each other and behave as two gases that are ideal, which are defined as dry air and water vapor.
Wind speed in relation to height (\(U_2\)): This process is used to calculate evapotranspiration and thus to define how it varies over time, for this, it is necessary to express it as the average of a defined interval in time as a function of time velocity.
Extraterrestrial radiation (\(R_a\)): This variable is obtained on a surface that is at the top of the atmosphere when it receives daily solar radiation.
Solar radiation (\(R_s\)): It is the process by which hydrogen reactions are obtained, emanated by the nucleus of the sun during nuclear fusion, and thus emitted to the solar surface, all this is obtained from the energy coming from the sun.
Net solar radiation or long-wave (\(Rl_N\)): The amount of long-wave energy emission proportional to the absolute surface temperature is raised to the fourth power. The net flux of energy leaving the Earth’s surface is less than that calculated and given by Stefan Boltzmann’s law due to absorption and reflected radiation from the sky.
Net radiation (\(R_n\)): is the process by which all the fluxes obtained from the radiation are added up, there are two values, short wave, and longwave, also taken from those coming from the surface.
Density of soil heat flow (\(G\)): In this process, the amount of energy transferred through the soil is measured, it is estimated when the soil heats up, as this depends on the net radiation.
ET of the crop under standard conditions (ETc) is the calculation of the ET of any crop when it has optimal soil conditions, abundant fertilizer, and without diseases. It is calculated from climatological data.
To make irrigation systems in hydroponic crops, it is necessary to analyze the space and the type of plant. The water requirement required for a crop will depend on both the baseline ET rate pattern and the distribution of the crop coefficient curves for the crops of interest during the growing season [10].
Hydric Estimation
In water estimation, is necessary to know the inputs and outputs in order to subtract the outputs and added the inputs. We used four inputs in the water estimation: previous irrigation, precipitation, capillary rise, and surface drainage. To calculate the water in the irrigation we based on the system DSSAT1 and models of water use for crops [10], [11] respectively.
Related Work
According to our statement of the problem, we search articles where: 1. Articles that discuss electronic prototypes that determine the specific amount of irrigation per plant. 2. Articles that present prototypes to schedule the irrigation with a graphical interface to the farmers. The related work is presented as follows.
Gocic et al., [12] created software in order to estimate the ET of reference using weather information. The authors present a user-friendly software that helps to calculate the Et0. The authors did not present a hardware device to generate the irrigation in the crops.
Zhang et al., [13] developed a scheme that brings together hardware and software, in order to calculate ET in real-time and through different processes to define automatic irrigation, based on the crop period and climatic aspects. To obtain the information, a hardware component was implemented that sends the recorded data to a server where irrigation is managed. The device used to irrigate the crop is in charge of determining the right moment to irrigate, on the other hand, it performs the calculations corresponding to the water balance, with the ET obtained. The approach of our project validates the factors individually in each plant, thus obtaining more accurate values.
Shah et al., [14] built a wireless sensor network (Wireless Sensor Networks) to be implemented in a grape crop. The objective of this research is to strengthen the requirements for optimal irrigation, in order to contribute to water saving. The sensors were placed in an area of 30m x 30m. Each of these sensors could receive and send information to each other within a defined distance of 30m. The network of sensors is responsible for obtaining data on soil moisture and pH, as well as collecting the ambient temperature. With this information collected, a node defined as the main one is in charge of making decisions in the defined area. In our research, the fact of implementing a sensor network would not be easy because of the type of crop, so our approach implements sensors that move to each of the crop plants.
Umair et al., [15] describe the implementation of a neural network that can control an irrigation method. Sensors that are installed in the crop obtain the inputs. The objective of such a method is to be able to maintain adequate moisture, taking into account the real-time moisture collected from the soil. Finally, they mention that the capabilities of the network to control are not as expected, which becomes a limiting factor to successfully completing the implementation.
Shamshirband et al., [16] use the Cuckoo search algorithm (CSA) to optimize the estimation from the artificial neuronal network (ANN) and the adaptive neuro-fuzzy inference system (ANFIS) models to calculate the evapotranspiration. The authors compared the algorithms to calibrate the evapotranspiration equation. The authors did not discuss the implementation of irrigation in any crop.
Suciu et al., [17] developed an irrigation system that collects information on air, temperature, plant evapotranspiration, soil moisture, frequency of precipitation, wind direction, and relative pressure. Such a system is able to control the irrigation systems according to the time determined by the information previously collected from the various sensors. But it is still up to the farmer to decide how much water to irrigate.
Prisilla et al., [18] discuss other irrigation systems that use the fixed rate for irrigation and do not use a necessary quantity of water for the crop. The authors created a system using an Artificial Neural Network (ANN) with the next parameters: air, temperature, soil moisture, radiations, and humidity to calculate the water in a rice crop. The ANN model also requires evapotranspiration to generate the water estimation. The authors only crated hardware to control the irrigation, the farmer is not interactive with the system.
Proposed Approach
The proposed system is integrated with several components that communicate to estimate water and schedule irrigation. The software components have the function of controlling the sensors, managing the data on the server, and presenting the views to the user so that the farmer can schedule the irrigations. The hardware elements are mainly sensors, devices to manage the water in the plants, and devices to move to each plant.
Components of system
In the proposed system each component has a unique function. In some cases, the component must communicate with another component. The interaction of the system components can be seen in Figure 1. The Central System and the Client Application are software components. The first one allows managing the database and calculating the evapotranspiration. The second one is a visual interface to farmer interaction. On another hand, the Master Component and Slave Component are electronic components. The first one is the handler of the next operations: irrigation, sensing the soil/temperature, and moving to a certain plant. The second one is the device that makes the action that the Master Component sends it. Next, the four main components in the proposed system are explained.
Central system. The objective of this component is to store the system data and generate the irrigations that have been programmed by the farmer. This component has different web services. The web services are mainly for the Client Application component and the Master Component.
The Central System Component was made with the NodeJS 2 language and MongoDB3 was used to store the data. MongoDB is a non-relational database. Mainly, the Central System Component has two subcomponents: a) REST API. It is responsible for managing HTTP requests, programming temperature measurements (to calculate Eto), and generating scheduled irrigations. b) Cloud DB. it is a database in MongoDB. The REST API and Cloud DB subcomponents connect over TCP/IP.
Client application. This component was made with VueJS4. The main objective of this component is to generate the views so that the farmer can interact with the system. The main actions that the farmer can carry out are: to view the water used in the crop, program irrigation, create plants and apply irrigation. This component communicates with the Central System Component using web services and the HTTP protocol.
Master Component. This component is an Arduino that is on the crop but must be connected to the router to access an internet connection. The main objective of this component is to review if any operation should be carried out on the crop. To do this, the Master Component must be connected with a web service from a Central System, if there is an operation to be carried out, the Master Component sends the necessary data to the Slave component so that it can carry it out. This component has the following subcomponents:
System controller. It is the base system of the Arduino.
Ethernet component. It is an electronic device (Ethernet Shield) connected to the Arduino to be able to communicate with the internet.
Bluetooth component. It is an electronic device to carry out communications with the Slave component.
Manage Operation. This is the software logic created to be able to read the operations of the Master Component and send the operations via Bluetooth to the Slave component.
Slave component. This is a custom artifact created to measure the ambient temperature and go to the plant to essentially carry out two actions: measure the state of the soil and apply irrigation. This component operates in the crop moving to the plants with coordinates.
Electronic devices
The proposed system has different electronic devices in order to measure data and generate communication with other components. The Master and Slave components are integrated by the next electronic devices. Figure 2 shows the electronic devices for Master and Slave components. Next, the electronic devices in the Master and Slave components are explained.
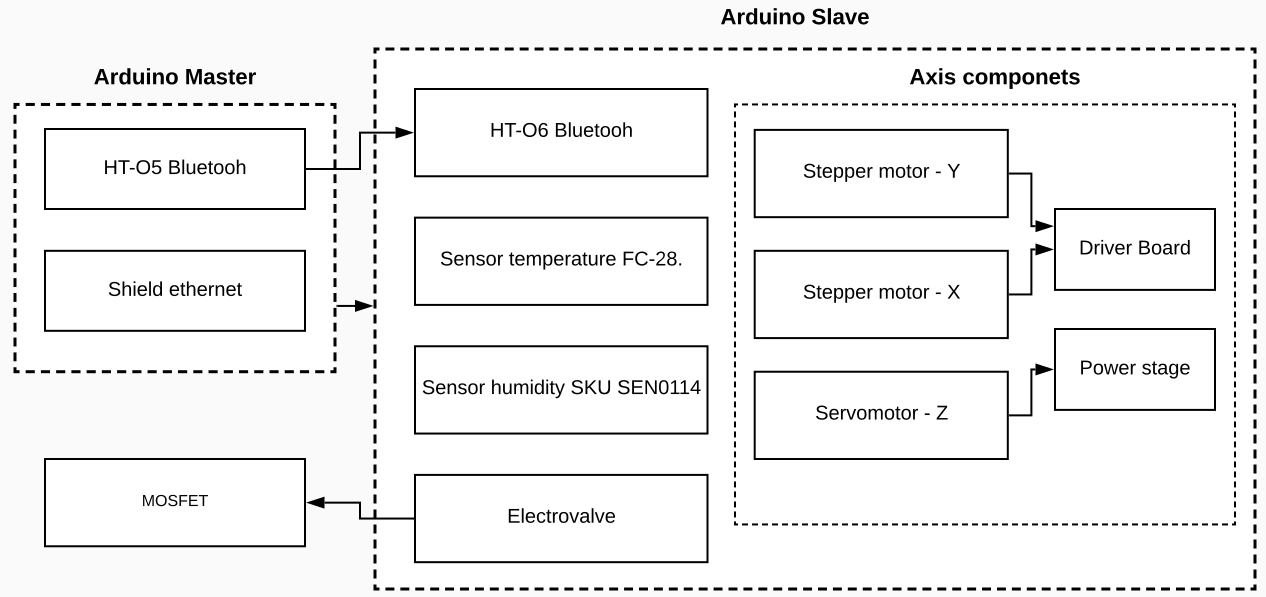
Master Component. Arduino Uno5 is the base in this component. To Bluetooth connection, we used an electronic device HC-05. For Ethernet connection, we used an Arduino Shield.
Slave Component. Arduino Mega6 is the base in the slave component. In Arduino Mega there are two sensors connected: humidity FC-28 and temperature DHT11. Also, like the Master Component, the Slave Component has a Bluetooth device HC-06. The Slave Component also includes two motors the type stepper each one is for the x-axis and y-axis. Moreover, the Slave component has been connected to a servomotor for the z-axis. Finally, for irrigation purposes, the Slave component has been connected to a solenoid valve that works at 12 volts.
Hydric Balance Process
The system proposed can irrigate each plant. For it, is necessary certain data to calculate the Eto and water estimation. Figure 3 presents the data necessary for the irrigation and the principal elements are explained as follows.
Data from DB. it is the parameters configured for a certain crop and stored in a database. The data are about the type of plants, ideal factors (temperature and humidity), specification in distance, and diameter of roots of the plants, among others.
Data required measurements sensors DB. It is a reading of sensors to get the current temperature and humidity from the Slave component. The Slave component can read data for a certain plant.
Process in the Central System. This element is the process to establish the water estimation in the system. The first step is to calculate the Eto. Next, is necessary to calculate the Etc. Finally, with the net irrigation and ideal irrigation, the final result is the volume of water for irrigation and the time necessary to on the solenoid valve in order to shoot water in the plant.
Evapotranspiration reference ETo: Evapotranspiration of reference consists of four inputs and one output, which is the ETo. Equation 1, which is FAO Penman-Monteith [19], was implemented for time periods.
\[ET_{0}=\frac{(0,48 \Delta(R_{n} - G) ) + (\gamma \frac{37}{Thr + 273} u_{2}(e^{0}(T_{hr})-e_{a}) ) }{\Delta +\gamma (1+0,34 u_{2})} \\ \label{}\]
where:
\(ET_{o}\)Reference evapotranspiration (mm \(hour^{-1}\))
\(T_{hr}\)Air temperature in one hour (\(^\circ\)C)
\(G\)Density of heat flow in the soil (MJ \(m^{-2}\) \(hour^{-1}\))
\(R_n\)Net radiation of the crop surface (MJ \(m^{-2}\) \(hour^{-1}\))
\(\gamma\)Psychometric constant (kPa \(^\circ\)\(C^{-1}\))
\(\Delta\)Slope of the steam precision curve (kPa \(^\circ\)\(C^{-1}\))
\(U_2\)Wind speed at a height (\(m s^{-1}\))
\(e^0(T_{hr})\)Pressure of vapor saturation at air temperature (\(k Pa\))
\(e_a\)Real steam pressure (\(k Pa\))
The temperatures Max - Min are used to calculate \(Thr\). Based on that, we can calculate \(e^0(T_{hr})\), the saturation pressure (\(e_s\)), and also the steam pressure (\(e_s-e_a\)). From this, the average temperature is used to calculate the slope of the steam precision curve (\(\Delta\)). In order to calculate whether data depend on the location of the crop, the information in the database regarding sea level and longitude-latitude coordinates are used. Based on this information, we can also calculate the extraterrestrial radiation (\(R_a\)). Finally, the ETo is calculated.Evapotranspiration of the crop under standard conditions ETc: It refers to the crop with the following conditions: no environmental factors, good fertilization, and good conditions for crop development. Then, the input crop coefficient (\(K_c\)) is used to relate the ETo with the ETc, which generates an output that corresponds to ETc.
Planting area: It is the third process of water balance, which consists of three inputs and one output. The first input is Diameter of roots (\(r\)) used to determine the floor area used by each plant. The second input is Row distance (\(dh\)), which is the distance covered by each row. The third input is Distance between plants (\(dpl\)), which defines the distance between plants in the row. Based on these, the result of the planting area is generated.
Net irrigation: The fourth process consists of five inputs. The first input comes from \(ETc\), which in the water balance is the main loss of water. The second input is the last humidity, which is obtained from the prototype before calculating the irrigation. Based on this, the calculation of the \(Eto\) is validated. The third input is irrigation coefficient (\(K_r\)), which determines the performance, transportation, and failures in the irrigation. The fourth input is Runoff coefficient (\(K_e\)), which is related to the precipitation (\(P\)) of rain that the crop has had as an additional water gain. The last input is the last irrigation, which is the last amount of water applied.
Ideal irrigation: It is the fifth process to perform. It consists of two inputs: the first input is the temperature at the time of irrigation and the second input is ideal factors stored by the plant (humidity, temperature, and amount of water). Based on them, we know whether or not the plant is in condition to receive irrigation.
Final result: If it is necessary to water the plant, the final result is the calculation of the time in which the device will irrigate. It is determined by the volume of the hose and according to the flow or quantity of water calculated in the previous steps.
Crop water needs
Crops need the water retained in the soil for their biological processes. The need for water for each plant increases with the growth of the plant since it varies from the sowing date to the day of harvesting. The need for water can be defined as the volume of water required. The water balance is the process of subtracting the outputs and adding the water inputs. Table 2 presents the inputs and outputs of a crop.
Inputs | Outputs |
---|---|
Precipitation | Evapotranspiration |
Amount of water in previous irrigation | Percolation losses (Filtration of water through deep layers of the soil) |
Capillary ascension (the ability of water to ascend through channels) | Outlet drain |
Evapotranspiration to crop (ETc)
In excellent conditions, the crop should be fertilized, free of diseases, and without moisture limitations in the soil. Evapotranspiration that occurs in a cultivated area can be measured directly through mass transfer methods using crop evapotranspiration. To calculate ETc, we use the following equation:
\[ET_{c}= K_{c}ET_{0} \\ \]
Where \(K_{c}\) is the crop coefficient. \(K_{c}\) is determined by various crop factors such as development stage, climate, and plant type. Table 3 shows the experimental values used in the software to establish the \(K_{c}\) value. The farmer can choose the type of need to \(K_{c}\) for a certain crop.
Type of water need | Value for (Kc) |
---|---|
Very low | 0.3 |
Low | 0.5 |
Moderate | 0.9 |
High | 1,2 |
Net irrigation (\(\Theta\))
Net irrigation is the amount of water suggested from evapotranspiration. To calculate the net irrigation it is necessary to obtain the water requirement of the plant (Da). The water requirement of the crop can be expressed in \(m^3/hour\) and is calculated with the following equation.
\[D_{a}=10\sum_{d=1}^{lp} \frac{\left ( \left ( K_{c} ET_{p}\right ) - \frac{p K_{e}}{100 }) \right ) A}{K_{r}} \\ \]
Where: the value 10 is the factor that is applied to convert Da to m3 / hour. lp is the duration of the growth period. \(Kc*ETp\) is the Evapotranspiration of the crop. P is the precipitation. Ke is the runoff coefficient. Kr is the coefficient of irrigation efficiency. A is the area planted. The proposed net irrigation (\(\ Theta\)) will be per day (lp = 1). The following equation allows you to calculate the net irrigation.
\[\Theta=A * 10 \frac{\left ( \left ( K_{c} ET_{c}\right ) - \frac{p K_{e}}{100 }) \right ) \Theta_{i} + H_{Sn} }{K_{r}} \\ \]
Where: \(\Theta_{i}\) is net irrigation from the previous day. \(\Theta\) is the crop water requirement \(m^3/hour\). Hsn is the soil moisture measured in the plant section.
Net irrigation using ideal factors per plant.
The ideal factors are established by the farmer in the software to establish the water that he would apply at an ideal temperature. To calculate the optimal total amount (RTop) the ideal amount of water (Rop), an ideal temperature (Top), and the current temperature at the time of irrigation (Tins) were used. Using the following equation, RTop can be calculated.
\[R_{top}= \frac{R_{op}T_{ins}}{T_{op}} \\ \]
The optimal total amount (RTop) would be the amount that the farmer would apply to irrigation in an ideal case. The optimal total amount is compared to the amount of irrigation that the software calculated (\(\ Theta\)) using evapotranspiration. Taking the variable that is greater, it will compare with the other and it will be added to eliminate estimation errors, then, if \(\ Theta\) <(RTop), the applied water will be:
\[Q_{ap}= \Theta + \frac{R_{top}}{100} \\\]
Else:
\[Q_{ap}= R_{top} + \frac{\Theta}{100} \\ \]
Time to irrigation
The flow (Q) is the volume of water that must pass through a surface in a given time. This section explains how the prototype determines the flow rate to irrigate a certain amount of water. The prototype uses a water flow sensor to allow the water to pass through. To find the flow, the conversion factor (Kcon) and the frequency (f) of the pulses with which the rotor of the water flow sensor is driven when the water passes through the mechanism were used. The frequency is calculated by: \(f = K_ {with} Q\). To calculate the flow, the following equation was used.
\[Q= fK_{con} \\ \]
To have a more accurate measurement it is necessary to calibrate the value of the conversion factor, this is done by doing experimental tests. It is done by: \(K_ {con} = \ frac {pulses} {V60}\). The volume (V) can be calculated as:
\[V= \pi r^{2} L \label{equ:10}\]
Where: r is the radius of the hose where the water comes out in the prototype. L is the length. To water with a specific amount, it will be done by calculating the time (seconds) in which the flow (water to be watered) needs to pass through the volume of the medium (hose). The calculated time (T) allows you to set the milliseconds with which the prototype should turn on the water flow sensor. To calculate T the following equation was used.
\[T= \frac{V}{Q_{ap}} \\ \label{equ:11}\]
System Coordinates
The device makes two displacements for calculating the water balance. The first displacement is made to read the humidity of the plant, while the second displacement is made at the time of irrigation. In the crop, each plant has a dropper, where the water is deposited to perform drip irrigation. There are three axes (x, y, z), where Axes x, y are used for the displacement \(\Delta x\) and \(\Delta y\) respectively. The axis z is used to irrigate. Figure 4 presents the Cartesian plane implemented in the crop. It illustrates two elements for the axis z: the first one is the electrovalve for the irrigation and the second one is the humidity sensor.
Communication between components
The client application has direct communication with the central system. Master and slave components communicate through Bluetooth using a data format created for this project in order to avoid data loss. Then, when the master sends information to the slave, the slave produces a response and vice versa; nevertheless, if the master or the slave goes offline, the response is not received; then, the action is sent again and when the offline device goes online they recover the communication to receive the data.
The central system responds using JSON format. Then, each component has a handler to generate this format depending on the type of response requested. The fundamental part of the project is in the communication between the master and the slave components. The Master Component is constantly consulting the REST API as well as the operations that are carried out in the future. Table 4 presents the data that the master must send to the slave to perform the operation depending on the type, i.e., humidity reading, temperature reading, go to plant or make irrigation. Once data is sent to the slave, it returns the responses of the response slave column.
Action (ac) | Data | Response from Slave |
---|---|---|
Temperature | ac | Measurement temperature |
Humidity | ac, Position (X, Y) | Measurement humidity |
Move to plant | ac, Position (X, Y) | ok |
Irrigation | ac, Position (X, Y), Time irrigation | Volumen water |
The central system handles the HTTP requests in the format JSON. The central system receives and returns JSON data. Then, each component has a handler to generate this format depending on the type of response requested. The most important handler is the central system, because, receives and sends JSON responses. Figure 5 presents the communication interaction in the central system. In the figure, the central system receives HTTP and Bluetooth requests, and depending on the data, the response can be in JSON or String with data.
Irrigation scheduling
This section explains step by step how the system performs the water estimation needed by each of the plants in the crop, with this already defined, it will be possible to program different risks according to the needs according to the data of each plant, in this way when programming the irrigation, the system will carry out this step by step automatically at the time determined by the system administrator.
Step 1: In this step the management of the plants is done, this means that we validate if there are already plants in our system, otherwise we create the plants that are necessary since we must have a record of all the plants that exist in the crop to make the corresponding measurements for each one. In addition, you can delete plants or edit their data.
Step 2: In this step the configuration of each plant is recorded, its most relevant requirements, such as the type of plant, its species, and the amount of water it needs, as this may vary depending on the species planted in the crop.
Step 3: In this step the mechanical device will move to the plant that we indicate from the system and will take the humidity of the plant, this data is sent to the system and is stored for further processing.
Step 4: In this step, the device takes the temperature of the environment, this data is stored in the system and together with the humidity it is possible to calculate the amount of water that the plant needs.
Step 5: In this step, the device makes the irrigation of the corresponding amount of water, based on the time obtained in the previous calculations, in this way, at the end of the irrigation time, the irrigation process of the plant is finished.
Each of the steps mentioned above is necessary for the correct operation of the device, also to obtain the correct calculation for each plant and thus apply the required amount of water. Then, the system can be programmed to do the step by step at a certain time every day or when it is required according to the species that are being planted, we call this the irrigation programming or scheduling.
Results
We performed a case study, which corresponds to the implementation of the system in one crop established in Bogota, Colombia, located at the coordinates: North Latitude: \(4^o35'56''\) and West Longitude: \(74^o04'51''\). Temperatures from December to March are high, averaging 20°, but from April to October they are lower, averaging 19° or less. The height at sea level is 2.625 meters. Tomato was taken as a study crop. The relative humidity ranges were between 70% and 80%. Root length density range was between 0.5 cm and 1.5 cm [20]. The ideal tomato temperature can be divided into three stages:
Germination. According to [21], the temperature for germination is between 16 and 30 degrees Celsius.
Growth development. According to [21], the temperature for growth development is between 12 and 30 degrees Celsius.
Fructification. The ideal temperature is between 15 and 22 degrees Celsius.
Then, in general, the values between 18.3 and 32.2 degrees Celsius were considered ideal air temperatures for tomatoes during the growing season [22].
We tested the system in a crop composed of thirty plants. The distance between rows was 0.7 meters and the distance between plants was 0.4 meters. The crop was observed from day 55 for the fructification stage. We studied ten plants of the thirty plants of the crop. Five plants were irrigated using the system, while the other five plants were irrigated manually. During 30 days the system made the water balance for the five selected plants and manual irrigation was carried out for other plants. The irrigation was done every day at 6:00 am by drip establishing different water levels.
Humidity is measured from 0% to 100%, where 0% means that the soil is completely dry and 100% is completely wet. Throughout the process of plant development, humidity must be maintained between 40% and 70% as ideal factors.
On the one hand, Figure 6 shows the humidity of the five plants irrigated manually, where the highest humidity was 98% achieved by the plants 2 and 3, while the lowest humidity was 0.3% achieved by plant 3. On the other hand, Figure 7 shows the humidity of the five plants irrigated by the system, where the highest humidity was 71.76% achieved by plant 5, while the lowest humidity was 39.63% also achieved by the plant 5.
With this in mind, we can observe that the humidity levels for the plants irrigated by the system are in almost all cases between the ideal factors i.e., between 40% and 70%, while the humidity levels for the plants irrigated manually are out of the ideal factors. Thus, based on the experimentation and the corresponding results, the system ensures a better irrigation process and also saves water in the crop.
In addition, Figure 8 presents the average (Thr), minimum (Tmin) and maximum (Tmax) temperature per day for this period of time. These readings were obtained by the sensor installed in the prototype. Thus, the temperature oscillates between 32.00 and 16.00 degrees Celsius.
Figure 9 presents the ETo readings in two time ranges: 06.00 - 07.00 (ETo1) and 14.00 - 15.00 (ETo2) during the thirty days. These results were dependent on Thr according to the min and max temperature readings 24 hours back. Then, in the crop the Eto2 was higher in the days 1 to 13, 16 to 21 and 28 to 30. For Eto1 it oscillated between 0.2 to 4.0 (mm/hour) and for Eto2 it had a variation between 0.9 to 4.6 (mm/hour).
Information system
The Client application is the system that the user can be interacting with. We named the Client application RIWA. This is the system that we provide to the farmers. Mainly, the farmer can easily register any plant in your crop. For the plant is necessary to set the name, name species, diameter or roots, and its ideal factors (humidity and temperature).
In RIWA, the user can register plants, view metrics about the water irrigation, establish crops variables, schedule the irrigations and make irrigation (right away). Figure 10 shows an interface of the RIWA system to present the water consumption of the irrigation by months.
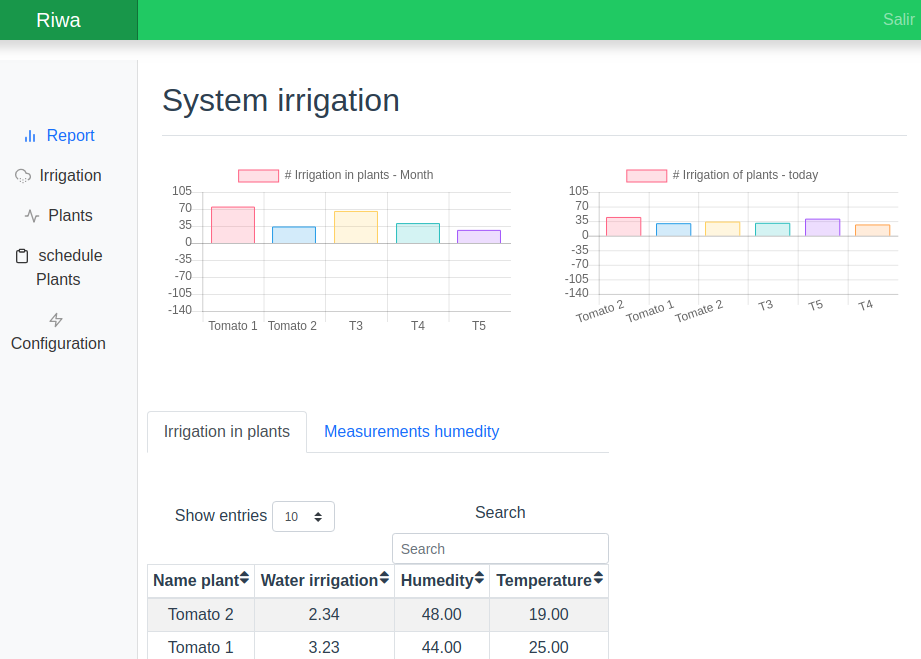
Discussion and Future work
Crops implementation. There is a huge gap between technology and agriculture in underdeveloped countries. Since the implementation of this would make the crops even more expensive, in addition to that, farmers refuse to try to change their way of producing, but we believe that everything is a process. With the use of technology in the crops will be even easier for the promotion of urban agriculture. Thus, farmers will be able to opt for change and implement technology, with this they will be able to have greater control of the crop remotely, which will not require the investment of large water resources.
Robot to go plant to plant. We show that the approach allows performing the function of estimating and watering the plants, solving the problem of calculating a good use of water. We try to make the software system very practical and intuitive so that farmers can interact without any problem.
At first, it was thought to build a robot to go plant to plant, due to cost and energy issues using the robot, this idea did not give results. To solve cost issues, the prototype is transported plant to plant by means of metal guides lowering to the floor of the plant to take the sample. The proposed approach allows going plant to plant with the limitation that if the plant has a high proportion, the metal guides must be changed since the sensor would not reach the ground. This approach saves the purchase of sensors per plant.
Water analytic. This point presents the future work. Water quality is a not factor used in this approach. Water quality refers to the characteristics of a water supply that will influence its suitability for a specific use, i.e. how well the quality meets the needs of the user [23]. The idea is to establish the water quality in each crop after a month’s use system. Thus, the farmer can know if the water is good or not through the water quality index (WQI). The idea is to create a new artifact to measure the required attributes (phosphate, Nitrates, etc. ) to establish the WQI. The new artifact must be integrated with the main system of this approach.
Conclusions
With the system, together with each of the electronic devices and software components explained, the agrarians can have a significant tool to irrigate their crops by making a water estimation to make a precise water use. In addition, the system explained favors the work of the farmers, since they do not have to irrigate every day because the system enables programming the irrigation for the plants making the validation of whether to irrigate or not by calculating the water needed for each plant.
In the system, the farmers can adjust certain parameters of soil and factors of the plants in order to control the water estimation. The evapotranspiration was calculated in each water estimation with hour time intervals. In that order of ideas, the Eto range was [0.2 4.6] mm/h in the studied crop. The humidity range was [40% 70%] (optimal). The water estimation was 2% for the crop because the general soil and plants were equal in the studied time of the crop.
ETo estimations establish that irrigation for the crop location and the species studied is best done in the morning when temperatures are low, this generates a lower water use because water loss by evapotranspiration ETo is lower.
Water is a very important factor in life. Most of the processes use the water to generate something, therefore, it is pertinent to interact technologically to contribute to saving water. The ideal factors of a plant (humidity, temperature) do not determine the amount of water to irrigate, in addition to these, the soil intervenes, which is the one that retains the water. To really calculate the water you have to measure the soil factors.
Authors' Information
Jorge Hernandez is a master’s student of information and communication sciences at the Universidad Distrital Francisco José de Caldas. His research topics are internet of things, artificial neuronal networks, dynamic behavior, and machine learning
Karen Daza is an undergrad student of telematic engineering at the Universidad Distrital Francisco Jose de Caldas.
Authors' Contributions
Jorge Hernandez designed and implemented the algorithm for the operation of the device, worked on the generation of the results, and participated in the writing of the article.
Karen Daza conducted a literature review of the main components of the device, collaborated in the analysis of the results, and participated in the writing of the article.
Competing Interests
The authors declare that they have no competing interests.
Funding
No funding was received for this project.